Switch-mode Power Supply for a Tube Car Amplifier
(c) klausmobile 2001
Design goals
- +11.0 ... +15.0 V input power supply, undervoltage
protection under +11V
- Low-dropout linear heater supply regulated to +11.5 ..
+12.0 V (series-wired 6V filaments), 3A (scalable up or
down)
- Regulated DCDC plate supply +250..+270V, 300mA, fully
isolated from chassis or power input, DC impedance less
than 10 Ohm
- Plate supply powerup delay - 20..30s upon REM IN signal
(turn-off immediately as REM IN is turned off)
- Muting relay ebable delay 3..5s upon plate supply powerup
(turn-off immediately as REM IN is turned off
- Maximum 3W power dissipation on any transistor to
simplify heatsinking. In my design, instead of a
dedicated heatsink, the PCB is simply bolted tightly
against chassis bottom which is the only available sink.
Heater supply and timers
To minimize heat loss on any transistor, I use two pass FETs.
In the car, input voltage is either 11.5-12.5V (engine off) or
13.5-14.5V (engine on). In the first case, T1 and T2 are fully
ON, no need for heatsink. In the second case - T1 is OFF, T2 ON,
all voltage and power excess is released across R5, no heatsink
necessary for FETs. However, when input is in between (13...14V)
- T1, in a linear regulator mode, may dissipate up to 3W (for a
3A load current).

Parts choice/substitutes:
- Optocouples may be any FET or bipolar output, rated to
5mA output (except for the upper half of IC5) . Upper IC5
optocouple sources power supply to PWM controller IC,
which is around 20mA.
- Т1-Т3 сan be any low-voltage FET, Rds<0.1Ohm. I
used IRFI540, IRFI9630 - whatever was in a box. Note that
I always prefer fully insulated TO220 devices (IRFIxxx
code) - this simplifies placement a lot.
- T2-T3 may be of logic-level or 'normal' type FET. T1 must
be 'normal' type FET only.
- T3 can be a bipolar PNP type (adjust R12,R13 for proper
base current).
- C2 can be anything from 470uF up - it's main purpose is
to prevent oscillations.
Plate regulator
I use UC3825 controller chip because it needs no external gate
driver, minimizing parts count. Current-mode control is not
necessary: in 12V networks, the transistors have at least 5x
current margin, so in case of a bad short they will survive
before the fuse blows. UC3825 is clocked at 180kHz
(transformer-dependent). Filter is a ladder CRCRC (no L's!),
voltage feedback is drawn from the second C in this chain. Such
arrangement, together with a low error amplifier gain, guarantees
stability.R120-T1-D107 current varies within 0-4mA range, so this
network itself is an additional shunt regulator (with very narrow
dynamic range).

Parts choice/substitutes:
- T101-102: Any normal (i.e. not logic level), 40-60V N-FET
with Rds<15mOhm. 6 mOhm devices need no heatsinks at
rated output. With IRFI1010 as used, dissipation is
around 2W per device.
- D101-102: IR's HFA06TB120 or any other ultrafast 3A,
1200V type
- C113: Propylen or other fast film type, 1 to 4uF
- All unmarked capacitors are 1uF surface-mount ceramic.
- IC102 Optocouple: Any NPN type, transfer ratio about
unity
- Transformer: 4.5 + 4.5 turns : 120 turns (that's
core-specific of course). I used a 34mm toroid, which is
quite an excess for 100W throughput, better use a smaller
ETD type core - much easier to wire.
Layout
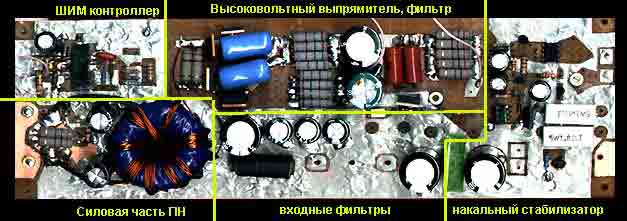
PCB size is 260*80mm, component footprint 250*60mm. Blue
snowflakes mark mounting holes for the three heat-sinked FETs -
they are soldered under the board. Total heatsink requirement is
under 10W. All HV network is surface-mounted on the upper side
(no vias or through-holes). T101,102 drains are soldered to
8*15mm contact pads on the upper side. Hot leads of transformer
primary and snubber R's are soldered to this pads too. Note that
C105, 106 and matching ceramic caps (1uF, SMD type) are placed
between T101,102 drains and transformer primary center tap - to
minimize AC current loop. The converter works fine with generic
(standard ESR) capacitors. The last capacitor (actually -
capacitor bank) is not on this board, but on amplifier PCB.
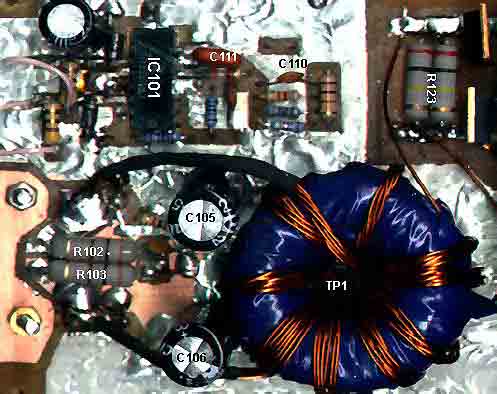
Source:http://www.klausmobile.narod.ru
-->